As a next step, I have ordered a second stepper motor for my more advanced prototype. This time, because I wanted to keep the size of the tap small, I ordered a Nema 17 pancake stepper motor. The difference is the height of the motor block, which is much thinner in this motor. After receiving the motor, I set up the second motor in the same way as the first and connected the new motor, a second motor controller and my Wemos board all together on the breadboard.
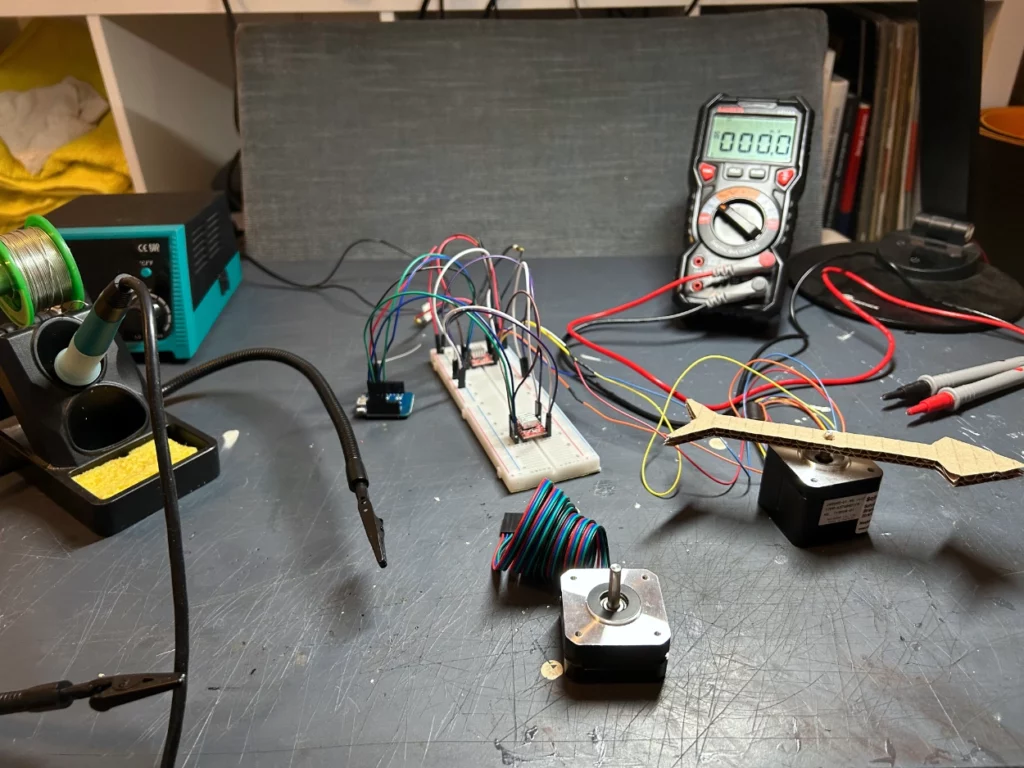
Two motor Mock-Up
Once everything was set up, I adapted the code running on my Wemos to control two motors instead of one, and tested two motors running in the same way as before the single motor. First in direction and interval and then in direction, acceleration and interval.
Results
After some problems with changing the code to allow for both motors to be driven at the same time, the set up was running quite smoothly. The only problem I ran into was that each of the motors required 1A at full power and my current temporary power source (a simple house-hold 12V plug-in transformer) only supplied 1.5A. This meant that as soon as I started playing around with faster speeds or resistance, one of the motors would miss steps, stop or just fail for a moment. So before I can really start building the first working prototype, I need to fix this problem. So my next step will be to build a custom power source that will provide enough power to run both motors at full speed.